SKD5 Tool Steel
SKD5 tool steel addresses the key challenge of tool failure in extreme temperature applications – scenarios where standard steels deteriorate rapidly. Manufactured through FCS Factory’s proprietary multiple refining process, this premium hot work steel has precisely controlled alloying elements that maintain structural integrity and hardness even when heated to 550°C in cycles. Industrial manufacturers using FCS Factory’s SKD5 consistently report 30-40% longer tool life in die casting applications, significantly reducing downtime and replacement costs while maintaining dimensional accuracy over long production runs.
The Japanese standard JIS SKD5 tool steel corresponds to the American standard H21, and the German standard ASTM is X30WCrV9-3/1.2581 tool steel.
SKD5 Tool Steel Product Introduction
SKD5 can be optimised to a hardness of 50-55 HRC and a predominantly martensitic organisation by high temperature hardening (oil cooled at 1075-1125°C) and specific tempering (multiple times below 400°C or above 680°C). The nature of the design relies on tungsten carbides for high-temperature strength, but is wary of the risk of toughness degradation due to grain-boundary impurity bias (e.g., arsenic, antimony), which needs to be modulated by the tempering process in order to balance red-hardness with resistance to brittle fracture.
SKD5 Tool Steel Types and Options
The table below shows the size range, surface condition and tolerance details for SKD5 Mould Steel:
SKD5 Tool Steel Customized Options
- Customized chemical composition: GB, DIN, ASTM, JIS and other standard grades can be produced. Chemical composition can be customized individually.
- Customized specifications: round steel (diameter), plate (thickness, width) can be customized production.
- Specialized packaging for long term storage or extreme transportation conditions: includes spraying black paint all around, wrapping plastic film, spraying anti-rust oil, and shipping in wooden crates.
- Customized production based on samples or technical agreements.
- SKD5 Tool Steel Electroslag Remelting (ESR): premium option with higher purity and isotropic properties for critical applications.
SKD5 Tool Steel Chemical Composition
SKD5 Tool Steel Heat Treatment Process
1.Annealing
2.Quenching
3.Tempering
4.Precautions
Heating process should control the rate of heating to avoid too rapid a rise in temperature leading to workpiece surface oxidation and decarburization. Protective atmosphere heating can be used or placed in the furnace charcoal and other anti-decarburization agent.
When quenching and cooling, choose the appropriate cooling medium and cooling method according to the shape and size of the workpiece to ensure the quenching effect while reducing the risk of deformation and cracking.
SKD5 Tool Steel Quality Inspection
1.Surface Condition Inspection
2.Chemical Composition Testing
3.Dimension and Tolerance Inspection
4.Hardness test
5.Ultrasonic Testing
6.Microstructure Inspection
(1) Metallographic Analysis
FCS factory will use metallographic analysis instrument to detect the microstructure state after heat treatment, including carbide distribution, martensite morphology, residual austenite content, etc.
(2) Grain size rating
SKD5 Tool Steel Technical Specifications
SKD5 Tool Steel Product Applications
Main application scenarios
Hot Forging and Extrusion Tooling
SKD5 retains its mechanical properties and wear resistance in hot forging applications where the die operating temperature exceeds 400°C. A major industrial equipment manufacturer uses our SKD5 dies for hot forging of heavy mechanical parts, with a 42% reduction in die changes and a significant reduction in unscheduled downtime. The steel's excellent through-hardening properties ensure consistent performance even with large cross-section tooling.
Hot dressing dies
SKD5 combines high hardness with good toughness, making it ideal for hot dressing operations. A leading automotive supplier uses it for hot forging crankshaft dressing, where edge retention is 35% longer than with previous materials, and edge chipping and cracking are significantly reduced, even under extreme shock loads.
Plastic injection moulds (high performance polymers)
For the moulding of abrasive or high-temperature polymers such as PEEK, PPS and glass fibre reinforced nylon, SKD5 significantly extends mould life. A manufacturer of precision electronic components uses our SKD5 for complex connector moulds, where maintenance intervals are extended by 45% and part quality is improved due to the steel's excellent thermal conductivity and wear resistance.
HOT SHEAR BLADES
SKD5 combines wear resistance and toughness to excel in hot shear applications. One steel mill used our SKD5 inserts to cut red-hot steel billets at 900°C. They lasted up to three times longer than conventional tool steels, with significantly improved cut quality and reduced maintenance requirements.
Industry-specific applications
- Automotive: Transmission housings, engine blocks, structural components, powertrain parts die casting
- Aerospace: Precision forging moulds for titanium and nickel alloy parts, thermoforming tooling
- Consumer Electronics: Complex smartphone and tablet housings die casting moulds, heat dissipation parts tooling
- Heavy Machinery: Large-size extrusion moulds, earthmoving equipment parts stamping tooling
- Energy: Silicon steel transformer hot stamping tooling, high temperature polymer forming moulds Medical Tooling, high temperature polymer moulding
- Medical: High performance polymer precision moulding tooling for surgical instruments.
SKD5 Tool Steel Competitive Advantage Comparison
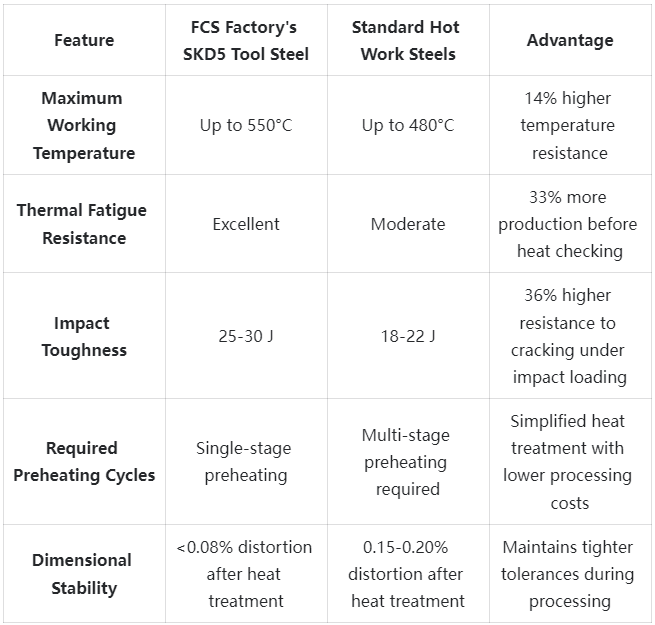
SKD5 Tool Steel Customer Success Stories
SKD5 Tool Steel Pricing Structure Information
SKD5 Tool Steel Frequently Asked Questions
Q: How does SKD5 compare to H13 (AISI) tool steel?
A: SKD5 is a Japanese Industrial Standard (JIS) grade and is very similar to AISI H13, both being chromium hot work tool steels. However, our SKD5 typically has a slightly higher vanadium content (0.8-1.2 per cent compared to 0.8-1.0 per cent for standard H13), greater wear resistance and a tighter control of the overall chemical composition, resulting in better consistency of properties. In practice, properly machined SKD5 has a service life of about 15-20% longer than H13 in severe hot work applications.Q: Can SKD5 be welded for repair or rebuild?
A: Yes, SKD5 can be welded using compatible filler materials such as H13 electrodes. However, the correct process is critical: preheating the material to 350-400°C, maintaining that temperature during welding, and post-weld heat treatment (tempering at approx. 550°C) to remove stresses. For critical applications, we recommend the use of matching SKD5 electrodes for optimum compatibility with the base material.Q: How does SKD5 perform in corrosive environments?
A: While SKD5 has some corrosion resistance due to its chromium content (4.75-5.50%), it is not designed for corrosion resistance. In applications involving corrosive media, we recommend additional surface treatments or consideration of our stainless steel hot work grades. For aluminium die casting, the natural oxide layer of SKD5 provides adequate protection, but for more demanding environments (e.g. copper alloy casting) a dedicated surface treatment is recommended.
Reviews
There are no reviews yet.