SKD2 Tool Steel
SKD2 is a high-carbon, high-chromium cold work mould steel conforming to the Japanese Industrial Standard (JIS G 4404-2006) and is classified as a Rheinitic steel among alloy tool steels. Its chemical composition is based on high carbon and high chromium, supplemented by molybdenum, manganese, silicon and other elements, while strictly controlling the content of phosphorus and sulfur impurities. It has high hardenability and low thermal conductivity (about 13.3 W/m-K at 23°C).
SKD2 forms a martensitic-based organisation after heat treatment by quenching (oil cooling at 960-1000°C) and tempering (180-350°C), with diffusely distributed chromium carbides giving it very high hardness and wear resistance (up to 62-64 HRC after heat treatment), but relatively low impact toughness.137 Its material hardness is 230-255 HBW in the hardened state, with high hardenability and low thermal conductivity (about 13.3 W/m-K at 23°C)1910 . Relatively low impact toughness. The essence of its material design is to use high chromium carbides to enhance wear resistance and dimensional stability, suitable for high load conditions at room temperature, but plasticity is limited.
FCS offers SKD2 tool steel to provide superior performance for high stress applications including drop dies, molding tools and precision cutting tools. It is available in a wide range of forms, including round and plate, and comes with custom machining and heat treating services.
SKD2 Tool Steel Product Introduction
SKD2 tool steel is a Japanese JIS standard high-carbon, high-chromium cold work die steel, belonging to the Rheinzite steel type, corresponding to German DIN grade 1.2436 (X210CrW12), American ASTM/AISI grade D2, and Chinese GB grade Cr12Mo1V.SKD2 tool steel excels in applications that require excellent wear resistance, high compressive strength, and good dimensional stability. FCS TOOL STEEL as a trusted supplier of SKD2 steel, we offer a wide range of general-purpose materials in various forms, including plates and round bars.
SKD2 Tool Steel Types and Options
The table below shows the size range, surface condition and tolerance details for SKD2 Mould Steel:
SKD2 Tool Steel Customized Options
- Customized chemical composition: GB, DIN, ASTM, JIS and other standard grades can be produced. Chemical composition can be customized individually.
- Customized specifications: round steel (diameter), plate (thickness, width) can be customized production.
- Specialized packaging for long term storage or extreme transportation conditions: includes spraying black paint all around, wrapping plastic film, spraying anti-rust oil, and shipping in wooden crates.
- Customized production based on samples or technical agreements.
- SKD2 Tool Steel Electroslag Remelting (ESR): premium option with higher purity and isotropic properties for critical applications.
SKD2 Tool Steel Chemical Composition
SKD2 Tool Steel Heat Treatment Process
1.Annealing
2.Quenching
3.Tempering
4.Precautions
Heating process should control the rate of heating to avoid too rapid a rise in temperature leading to workpiece surface oxidation and decarburization. Protective atmosphere heating can be used or placed in the furnace charcoal and other anti-decarburization agent.
When quenching and cooling, choose the appropriate cooling medium and cooling method according to the shape and size of the workpiece to ensure the quenching effect while reducing the risk of deformation and cracking.
SKD2 Tool Steel Quality Inspection
1.Surface Condition Inspection
2.Chemical Composition Testing
3.Dimension and Tolerance Inspection
4.Hardness test
5.Ultrasonic Testing
6.Microstructure Inspection
(1) Metallographic Analysis
FCS factory will use metallographic analysis instrument to detect the microstructure state after heat treatment, including carbide distribution, martensite morphology, residual austenite content, etc.
(2) Grain size rating
SKD2 Tool Steel Technical Specifications
SKD2 Tool Steel Product Applications
Main application scenarios
Drop and Stamping Dies
SKD2 tool steel excels in drop and stamping applications where edge retention and wear resistance are critical. A major automotive parts manufacturer uses our SKD2 drop dies for high-volume production, reporting 40% longer sharpening intervals and a 30% reduction in tooling replacement costs compared to the previous material.
Cold Forming Tools
SKD2's high compressive strength and wear resistance make it ideal for cold forming applications. An industrial fastener manufacturer used our custom machined SKD2 forming tools in a cold heading operation, significantly reducing the frequency of tool changes and maintaining consistent part dimensions, even after hundreds of thousands of cycles.
Cutting Tools and Shear Knives
For industrial cutting tools that process high-strength materials, SKD2 offers superior edge retention and durability. A metal fabrication facility uses our heat-treated SKD2 shear blades to cut stainless steel strip with less blade maintenance downtime and more accurate cuts than with previous tool materials.
Plastic Mold Components
SKD2 provides superior wear protection in plastic molding applications where abrasive fillers are present. A precision parts molder used our SKD2 inserts in glass-filled nylon components and reported minimal cavity wear and consistent part dimensions, even after millions of injection cycles.
Industry-specific applications
- Automotive manufacturing: stamping dies, trimming tools and forming dies for high-volume sheet metal parts.
- Aerospace industry: precision cutting tools, special alloy forming dies and measuring fixtures.
- Electronics manufacturing: progressive dies for connector assemblies and fine blanking tools for precision parts.
- Heavy machinery: wear plates, cutting edges and tools for high-stress parts.
- Medical device manufacturing: precision cutting tools and forming dies for surgical instruments.
SKD2 Tool Steel Competitive Advantage Comparison
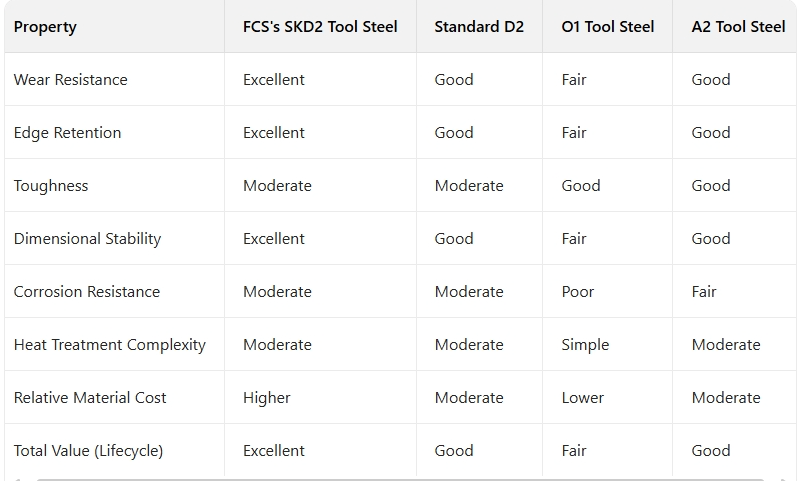
SKD2 Tool Steel Customer Success Stories
SKD2 Tool Steel Pricing Structure Information
SKD2 Tool Steel Frequently Asked Questions
Q: What are the main differences between SKD2 and regular D2 tool steels?
A: While both are high-carbon, high-chromium tool steels, SKD2 typically offers more consistent chemical control according to Japanese Industrial Standards (JIS), resulting in more predictable heat treatment response and performance characteristics. These materials are very similar and SKD2 typically exhibits slightly superior wear resistance in controlled tests.Q: How does SKD2 compare to SKD11 in cold work applications?
A. SKD2 typically provides superior wear resistance but is slightly less tough than SKD11. For high compression, high wear applications with minimal impact, SKD2 typically provides longer service life. Applications with significant shock loading may benefit from the enhanced toughness of SKD11.
Reviews
There are no reviews yet.